PT. Environeer
031-99858624 (Surabaya), 021-8935060 (Jakarta)
REQUEST A FREE ESTIMATE!
Transferring Plastic Cup Products Using Modular Conveyors
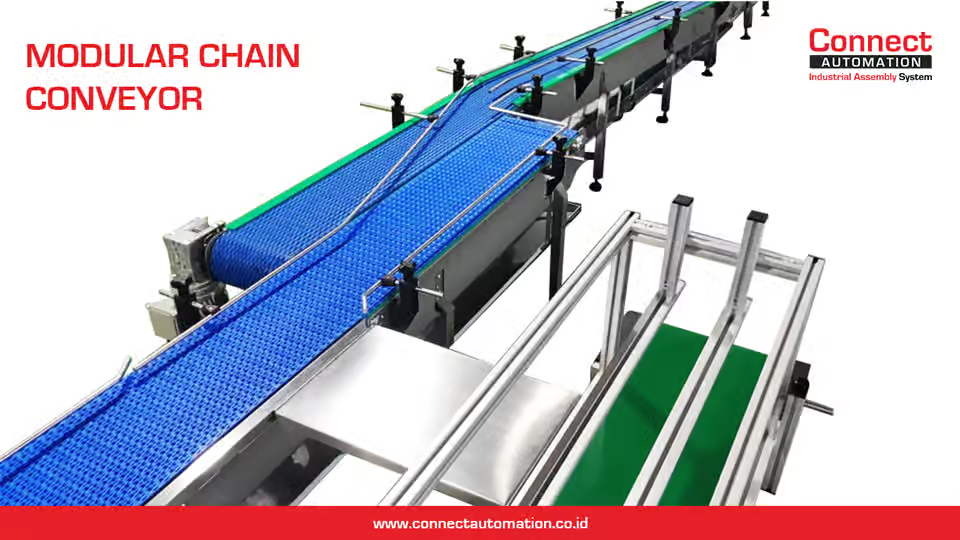
Conveyors can be made into any shape using variaties of materials for any uses in a production line. A Modular Chain Conveyor is no exception as it can be made for many purposes and like its siblings, Modular Chain Conveyor do have some strength and weaknesess that makes it unique to its siblings.
For instance, Modular Chain Conveyor uses an assembled plastic modules that functions as its belt. This means that if the plastic belt got damaged, the replacement wouldn’t be as expensive and takes less time to replace than a traditional Belt Conveyor.
Our customers wanted to transport sealed plastic water cups containing drinking water which produced from a machine to a packaging line consists of several packaging tables. The distance from the plastic cup producing machine to the packaging tables are about 15-20 meters long which would make it really hard to transport the plastic water cups manually. Our solution was to make them 2 Modular Chain Conveyors that runs in conjunction. These 2 Modular Chain Conveyors would transport the plastic water cups from within the machine to the packaging tables where people would pick the plastic water cups and pack them inside a packaging box.
How It Works
First conveyor receives the plastic water cups produced by our customer’s machine and then transported to the second conveyor. The first conveyor is a Curved Modular Chain Conveyor which basically would receive the products then curved it 90 degrees and then the rest is just straight Modular Chain Conveyor.
The second one receives the plastic water cups from the first Curved Modular Chain Conveyor and then the plastic water cups would be picked up by employees working on the packaging line and into the packaging box. The second Modular Chain Conveyor formed as Straight Modular Chain Conveyor unlike the first conveyor which has a 90 degrees curve in it.
These 2 Modular Chain Conveyors are a separate conveyors. So how does the plastic water cups goes from first conveyor to the second conveyor? Well we put a few meters of the end of first conveyor right next to the start of the second conveyor, leaving no gaps between them so the plastic water cups doesn’t fall down. Next one is we made a conjoined side guide that runs from the first conveyor to the second one, curving the plastic water cups to the second conveyor. This way, the plastic water cups would still have movement forcing it forward, while the side guides are curving (or directing) them onto the second conveyor.
Before
Our customer would’ve need to transport all of the water cups from the machine to the packaging area using trolley or they would need to move their packaging tables directly next to the machine for less effort. Even then, they are still moving their water cups manually and this creates motion and transportation waste.
After
No longer needing to move their packaging tables or the water cups manually, their production line runs most efficient using the 2 conveyors that does all the work for them.
Just with that, productivity of our customer increased by a ton. Our customer, as well as lots of other manufacturers are improving their productivity with us and they do not wait for others, so don’t be the one company who still uses trolley to move things, when people around the world are already using conveyors!
Do you want to know about our other conveyor types? (yes, we do provide multiple types of conveyors)
Your own productivity can be improved without any cost!
Read here if you want to know more.
About Us
Connect Automation specializes in providing automation solutions, including conveyor systems, to improve efficiency across various industries. The company delivers cutting-edge technology to help organizations automate tasks and optimize workflows. Connect Automation helps businesses reduce manual efforts, boost productivity, and achieve better outcomes. With a customer-focused approach, the company designs tailored solutions to ensure smooth and effective automation transitions for long-term success.
Connect Automation specializes in providing automation solutions, including conveyor systems, to improve efficiency across various industries. The company delivers cutting-edge technology to help organizations automate tasks and optimize workflows. Connect Automation helps businesses reduce manual efforts, boost productivity, and achieve better outcomes. With a customer-focused approach, the company designs tailored solutions to ensure smooth and effective automation transitions for long-term success.
Cikarang Office
Kawasan Industri Jababeka Tahap 1, Jl. Jababeka II D Blok C14L Cikarang, Indonesia (17530)
(021) 893 5060 Google Maps
Kawasan Industri Jababeka Tahap 1, Jl. Jababeka II D Blok C14L Cikarang, Indonesia (17530)
(021) 893 5060 Google Maps
Surabaya Office
Rungkut Industri III, No. 37, Rungkut Menanggal, Kec. Gn. Anyar Surabaya, Indonesia (60293)
(031) 9985 8624 Google Maps
Rungkut Industri III, No. 37, Rungkut Menanggal, Kec. Gn. Anyar Surabaya, Indonesia (60293)
(031) 9985 8624 Google Maps