Several tips and ways to operate the conveyors safely
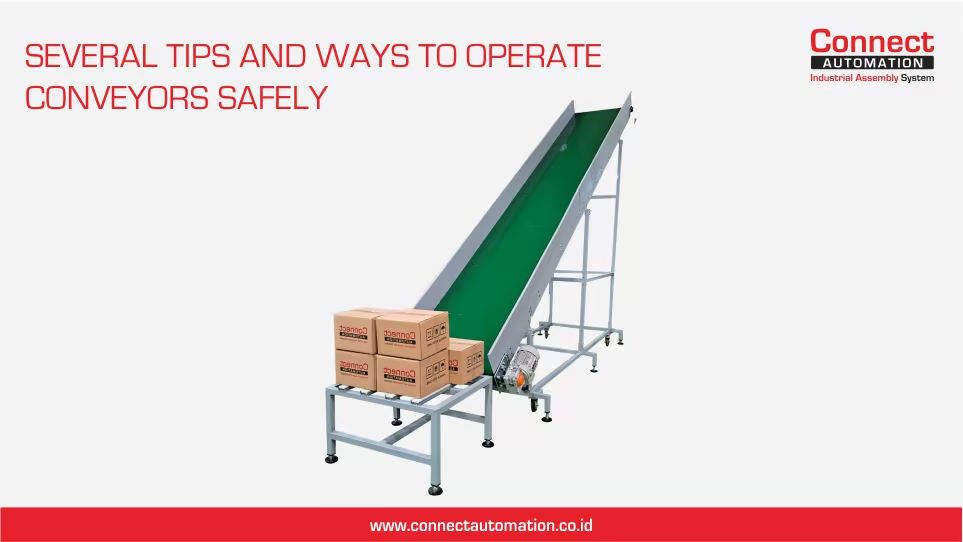
Tips to Operate Conveyors Safely
Transporting materials and products efficiently is a crucial aspect of numerous industries, and conveyor belts play a vital role in achieving this objective. However, it is essential to prioritize safety when working with or near conveyors to prevent workplace accidents and injuries. In this comprehensive guide, we will explore the best practices and precautions to ensure the safety of workers and maintain smooth operations in conveyor systems.
Common Issues in Conveyor Systems
Before delving into safety practices, let's first examine some common problems that can arise in conveyor systems and potentially pose safety hazards. By understanding these issues, we can take proactive measures to prevent accidents and maintain a safe working environment.
- Belt Damage. Harsh or abrasive materials can cause tears, frayed edges, and discoloration on conveyor belts. Such damage can compromise the integrity of the belt and lead to accidents.
- Blockages. When items get snagged or accumulate on the production line, blockages can occur, disrupting the flow of materials and potentially causing accidents.
- Slippages and Spillages. Worn pulleys, belt lagging, or excessive loads can result in materials sliding off the conveyor during operation, posing risks to nearby workers.
- Mistracking. If the conveyor belt is misaligned, materials may veer off track, increasing the likelihood of accidents and disruptions.
- Seized Rollers. Over time, conveyor system rollers can experience wear and tear, leading to sharp edges that can damage items on the line and pose safety hazards.
- Carryback. Material buildup in the system can create blockages, leading to malfunctioning and potential safety hazards.
Proactive maintenance and regular inspections are essential for identifying and addressing these issues promptly, preventing downtime and ensuring worker safety.
10 Do's and Don'ts of Conveyor Safety
To promote safety in conveyor operations, it is crucial to adhere to specific guidelines and industry best practices. The following list outlines the top 10 do's and don'ts for safe conveyor operations :
- Keep Clothes, Body Parts and Hair away from the Conveyor. One of the most common causes of conveyor-related injuries is contact between workers' clothing, body parts, or hair and the moving parts of the conveyor system. It is paramount for trained personnel to maintain a safe distance from conveyors, and visitors should undergo briefings on conveyor safety before entering the plant. Avoid wearing loose clothing, long hair, watches, bracelets, or rings that can get caught in the system.
- Don’t climb, step, sit, or stand on the conveyor. Under no circumstances should anyone climb, sit, stand, walk, ride, or touch the conveyor line. Although it may seem tempting or harmless, doing so can result in serious injuries. Conveyors are not designed to accommodate human presence, and pinch points and weight capacities can pose significant risks. Always prioritize proper safety protocols and avoid any actions that compromise personal safety.
- Ensure All Equipment Is Clean Before Starting. Conveyor systems should be equipped with warning signals that sound prior to startup, as mandated by OSHA standards. However, it is essential to go beyond this requirement and provide comprehensive training on the significance of the warning signals and the potential injuries that can occur if they are ignored. All personnel must be clear of equipment before starting it up to prevent accidents.
- Remove Or Alter Conveyor Guards Or Safety Divides. Guards and safety divides are critical components of conveyor systems, protecting workers from contact with moving parts. These safety measures should never be removed or altered, even during maintenance or repairs. Lock out conveyors when servicing them and operate the equipment only when all approved covers and guards are securely in place.
- Know The Location and Function Of Stop/Start Controls. Familiarize yourself with the location and function of emergency stop and start controls in the conveyor area. It is crucial to train all employees on the proper use of these controls, their locations, and the circumstances that warrant their activation. Clearly mark the controls to minimize confusion and enable quick decision-making during emergencies.
- Don’t Perform Service On A Conveyor Until The Motor Disconnect Is Locked Out. Before conducting any maintenance or repairs on a conveyor system, ensure that all electrical, air, or hydraulic power sources are disconnected or blocked out. Implement lockout/tagout systems to prevent accidental powering up of the equipment during service. Taking these precautions can prevent accidents and injuries caused by unexpected activation of the conveyor system.
- Do Allow Authorized Personnel to Operate/Maintain Material Handling Equipment. Only trained and authorized personnel should operate and perform maintenance on conveyor systems. Providing comprehensive training ensures the safety of technicians and promotes optimal conveyor performance. If necessary, seek assistance from professionals who specialize in conveyor maintenance and automation solutions to enhance safety measures.
- Don’t Modify or Misuse Conveyor Controls. Conveyor controls should never be modified or misused by unqualified individuals. While employees may attempt modifications to suit specific areas or functions, these alterations can compromise overall safety. Emphasize that conveyor controls are part of a larger system and any changes must be approved by management to maintain a safe working environment.
- Do Make Conveyor Safety Training A Priority. Any facility utilizing conveyors should prioritize regular and comprehensive safety training for employees. Training programs should cover safe operation practices, emergency procedures, and prevention of unsafe acts. Regularly update and reinforce the training to keep employees informed about potential hazards and safe behavior standards. Extend the training to visitors who may be near the conveyor system to ensure a collective commitment to safety.
- Don’t Fail To Report Unsafe Conditions to Your Supervisor. Establish a culture of safety that encourages workers to report any unsafe conditions they observe, such as loose guards or workers in close proximity to the conveyor system with unrestrained clothing or hair. Provide training on safety issues and emphasize the importance of reporting unsafe practices, equipment malfunctions, or potential hazards. Encourage anonymous or no-consequence reporting to ensure prompt action and maintain a safe working environment for everyone.
By following these do's and don'ts, you can significantly reduce the risk of accidents in conveyor operations, promoting a productive and safe working environment.
Conclusion
Conveyor systems are invaluable tools in various industries, but their safe operation is paramount to prevent workplace injuries and accidents. By implementing proper safety practices, conducting regular inspections, and providing comprehensive training, companies can ensure the well-being of their employees and maintain efficient conveyor operations. Prioritize safety in every aspect of conveyor use, from personal protective equipment to adherence to safety protocols, and create a culture where safety is a shared responsibility. Remember, a safe workplace is a productive workplace. Connect Automation is available to assist your company in choosing the right conveyors and optimizing safety practices.
Get FREE consultation with our sales engineer team!
Appoint a Consultation
Connect Automation specializes in providing automation solutions, including conveyor systems, to improve efficiency across various industries. The company delivers cutting-edge technology to help organizations automate tasks and optimize workflows. Connect Automation helps businesses reduce manual efforts, boost productivity, and achieve better outcomes. With a customer-focused approach, the company designs tailored solutions to ensure smooth and effective automation transitions for long-term success.
Kawasan Industri Jababeka Tahap 1, Jl. Jababeka II D Blok C14L Cikarang, Indonesia (17530)
(021) 893 5060 Google Maps
Rungkut Industri III, No. 37, Rungkut Menanggal, Kec. Gn. Anyar Surabaya, Indonesia (60293)
(031) 9985 8624 Google Maps